More than 250 years ago, a revolution was underway in Britain – not that anyone realized it at the time. For centuries, communities had been forced to painstakingly produce goods by hand but a new way of working was changing the game. Instead of relying solely on human and animal power, people were increasingly using water and steam power to build finished goods and enable mass production.
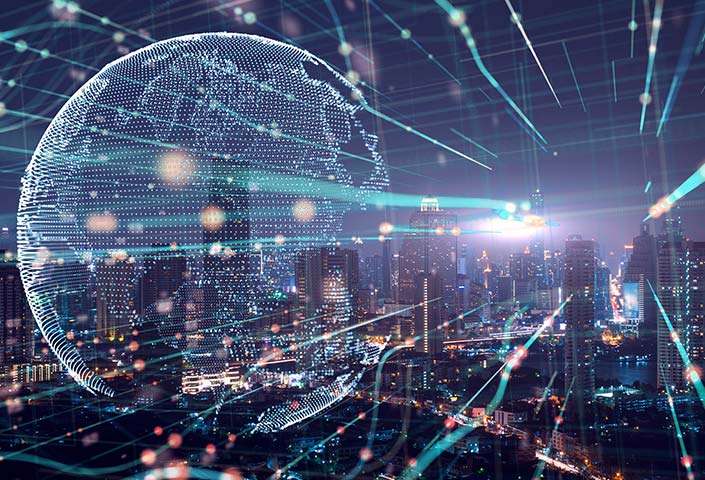
It was not until an English economic historian by the name of Arnold Toynbee (1852-83) popularized the term ‘Industrial Revolution’ that the period received an official title for the manner that it had transformed society. Although used earlier by French writers, it was Toynbee who cemented the perfect way to describe the process of change that had driven Britain’s economic development from 1760 to 1840.
How times have changed.
Where it took decades for the likes of Toynbee to identify and label the history-shaping events of the first industrial revolution, we now live in a world that wastes no time in not only recognizing that monumental change is unfolding before our eyes but studying the best ways for businesses to benefit from it.
We even have a modern-day vocabulary for naming it – hence the dawn of Industry 4.0.
What is Industry 4.0?
There are no prizes for guessing that Industry 4.0 is the name given to the next major phase of the industrial revolution, which has its roots in manufacturing but is spreading quickly across all sectors and industries. While there is no single definition of Industry 4.0, the term describes a move towards digital transformation in business and is often used interchangeably with ‘smart manufacturing’ and ‘digital manufacturing’. It essentially refers to an industrial or business environment where machines can bridge digital and physical worlds, exchange information with each other and with people, and collect, analyze and act upon real-time information.
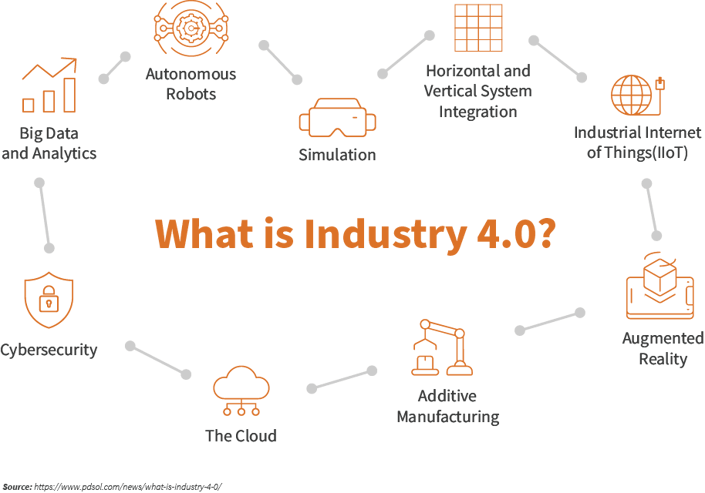
Historical context
Before immersing ourselves in the characteristics and business principles of Industry 4.0, it is worth engaging in a brief history lesson to appreciate how we have arrived where we are. Each of the industrial revolutions has had an enormous impact on society, changing how people worked and the ability of businesses to deliver goods and services.
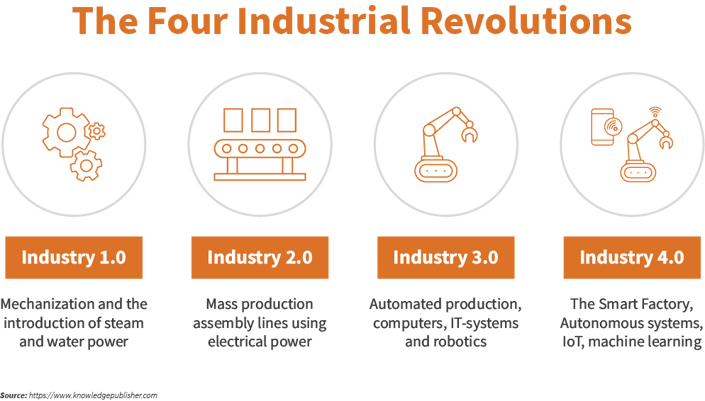
- First industrial revolution: starting in Britain and spreading to the rest of the world, the first industrial revolution ran from 1760 to 1830 and saw manufacturing evolve from manual labor performed by people and animals to an optimized form of labor. It largely centered around machinery powered by water and steam engines, reducing the physical toll on human workers and enabling mass production of manufactured goods.
- Second industrial revolution: fast-forward to the late 19th century and the introduction of assembly lines and use of oil, gas and electric power delivered huge benefits for mass production in factories and beyond. The new power sources made manufacturing more efficient, while improved communications via telephone and telegraph were another boost for businesses. The second industrial revolution is widely considered to have run from 1870 to 1914 (the start of World War I).
- Third industrial revolution: starting in the late 1950s, the third industrial revolution signaled the emergence of computer technologies into factories and an increased focus on digital technology and software. Adding advanced telecommunications and data analysis into manufacturing processes helped automate some processes and increased the ability to collect and share information.
- Fourth industrial revolution – aka Industry 4.0: the 21st century has seen many of the most incredible technology advancements in history. The digital pioneers of the third industrial revolution would unlikely be able to fathom how far things have progressed in a matter of decades – and there is even a sense that Industry 4.0 is only just getting started.
The impact of Industry 4.0
Given a revolution is defined as “a sudden or momentous change in a situation”, it is fair to say Industry 4.0 fits the bill. The latest industrial revolution to sweep the world is revolutionizing how companies manufacture, improve and distribute their products, with previously unheard-of concepts such as the Internet of Things (IoT), cloud computing, artificial intelligence (AI) and machine learning now considered vital aspects of any organization.
Step into the modern factory and you will be overwhelmed by the amount of sophisticated technology that is providing access and insights from previously unattainable information. Advanced sensors, embedded software and robotics can collect and analyze data that allows for better decision-making, while digital technologies are leading to increased automation, predictive maintenance and self-optimization of process improvements.
Increased productivity and improved quality are goals of any executive and that is within reach via the use of high-tech IoT devices and AI-powered visual insights in smart factories. An example is the ability of sensors on the factory floor to provide large amounts of data for analysis, enable real-time visibility of manufacturing assets and, ultimately, ensure minimization of equipment downtime. Meanwhile, smartphones connected to the cloud can allow staff to monitor productivity and performance from almost anywhere, while machine learning algorithms can save costly repairs by detecting errors immediately.
Industry 4.0 technologies
While Industry 4.0 technologies have existed individually for a while, they have recently begun to influence and impact each other courtesy of the internet and significant reductions in cost. At a base level, they add value by allowing better visibility into manufacturing lines, supply chains and resource usage.
- Industrial Internet of Things (IIoT): the capacity to collect, analyze and exchange large amounts of data is a key feature of Industry 4.0 and the Industrial Internet of Things (IIoT) is the tool that is allowing it to happen in smart factories. Not to be confused with the consumer Internet of Things (which is about making people’s lives easier or more fun), it refers to the billions of industrial devices that are filled with sensors, connected to wireless networks and gather and share data. With even the smallest devices now able to be connected, the IIoT has the potential to enable faster and better decision-making by providing extremely detailed data in real-time. From gaining insights into how production lines are operating and predicting what machines need servicing to understanding where bottlenecks are in the supply chain, IIoT projects are paving a new forward for smart companies.
- AI and machine learning: for decades, companies have been forced to deal with industrial machines breaking down during the production process. Now imagine being able to perform predictive maintenance based on previously inaccessible insights into their operation. That is just one of the benefits of machine learning algorithms, which, along with artificial intelligence, is allowing companies to tap into volumes of information generated across their business units and even from partners and third-party sources. AI and machine learning is undoubtedly providing better visibility, predictability and automation of operations and business processes.
- Cloud computing: no Industry 4.0 strategy is complete without cloud computing. One of the key technological developments of the 21st century, it allows smart manufacturers to realize the connectivity and integration of engineering, supply chain, production, service and sales and distribution that is essential for modern-day business success. Along with reducing start-up costs for small and medium-sized manufacturers, cloud computing means large amounts of data that need to be stored and analyzed can be processed more efficiently and cost-effectively.
- Cybersecurity: just as a more digitally connected workplace is enabling more efficient manufacturing processes, it is opening new opportunities for costly cyberattacks and malware. For that reason, organizations committed to digital transformation in the era of Industry 4.0 need to prioritize the importance of cybersecurity platforms to protect their data, information and equipment.
- Digital twin: one of the unexpected benefits of Industry 4.0 has been the realization that manufacturers can create virtual replicas of their processes, production lines, factories and supply chains – in effect, digital twins. These are created by extracting data from IIoT sensors and other devices connected to the internet and can be used to help increase productivity, create new products and improve workflows. One example would be a manufacturer simulating a production process to test potential changes that may result in less downtime or increased capacity.
- Edge computing: lesser known but increasingly popular Industry 4.0 technology is ‘edge computing’, which refers to data analysis being done at the ‘edge’ or where the data is created. The pressure of production operations means some safety or quality issues may require near-real-time action and this is where edge computing comes into play. Rather than needing to send data to the enterprise cloud and back to the factory floor, it reduces the time from when data is produced to when such responses are required. Edge computing also reduces security risks by keeping data near its sources and decreases the need to depend on the reliability of external networks.
Industry 4.0 – survive and thrive?
It goes without saying that the thought of an industrial revolution can send a shiver down the spines of old-school executives. Such monumental industry-level changes can cause many to fear their sectors or organizations may become redundant but the reality is companies that adapt quickly can not only survive but thrive in the new world. Change is inevitable so the best approach is to consider the best way forward.
It is essential to embrace opportunities and tackle threats with a clear and precise plan. More importantly, one should not try to do it all at once. An important first step is to not only consider the areas of a business that should be changed but pinpoint the best time for doing so. Ask yourself how potential Industry 4.0 technologies can fit into your objectives and identify the best ones for helping you achieve your goals. Furthermore, predict what other industry-level changes may unfold in the coming years based on your expertise in the sector.
With many businesses having already started their Industry 4.0 transitions – and others accelerating their efforts in the wake of the COVID-19 pandemic – there is no time to waste. The technological solutions to improve productivity and increase efficiencies are well and truly available, with studies having shown that 39% of industry leaders having already implemented a nerve center or control tower approach to increase end-to-end supply-chain transparency and about 25% fast-tracking automation programs to stem worker shortages due to the pandemic.
Inside the Industry 4.0 Smart Factory
A concept closely related to Industry 4.0 is the Smart Factory, which is based on cyber-physical systems and designed to ensure a high degree of product customization and enable manufacturing processes to take place with minimal human interaction. Key features include:
- Data analysis: while the first two industrial revolutions changed the way people physically worked, Industry 4.0 is largely about providing unprecedented access to information. Sensors and interconnected machinery in workplaces are producing significant amounts of data that are allowing manufacturers to investigate historical trends, identify patterns and make better decisions. It does not need to end there either, with data from other elements of an organization and its suppliers and distributors creating even deeper insights. It has never been easier for managers to make production decisions based on sales margins and personnel.
- IT-OT Integration: operational technology (OT) is one of the buzzwords to arise from Industry 4.0 and relates to the technology used for connecting, monitoring and securing an organization’s industrial operations. While IT focuses on a company’s front-end informational activities (eg: email, finance, HR), OT centers on back-end production such as robots, industrial control systems (ICS) and programmable logic controllers (PLCs). Crucially, a smart factory relies on strong interconnectivity between both areas, with real-time data collected from sensors, devices and machines on the factory floor needing to be seamlessly shared across other IT components.
- Custom manufacturing: when the first industrial revolution swept Britain in the late 1700s, workers and consumers realized the benefits of mass production. Now, with Industry 4.0 showing no signs of slowing down, it is mass customization that is dominating the conversation. Today’s smart factories can produce customized products that meet individual needs more cost-effectively, with manufacturers using advanced simulation software applications, new materials and technologies such as 3D printing to deliver small batches of specialized items for specific customers.
- Supply chain: few industrial operators can achieve success without access to a transparent and efficient supply chain and Industry 4.0 is reinventing how they resource their raw materials and deliver their finished products. Where deliveries were previously left to chance in many cases, the modern manufacturer can share production data with suppliers to ensure tighter schedules and happier customers. Take the example of a production line suffering an unforeseen disruption but that delay being offset by real-time updates that allow deliveries to be rerouted or delayed to reduce wasted time and money. Access to weather information and retail demand data also mean companies can use predictive programs to schedule completed goods to be sent at the perfect time for consumers.
- Areas of focus: Industry 4.0 technologies can make a significant impact across various areas of manufacturing but there are three main facets where many executives are choosing to invest.
- Operations: in previous decades, the likes of supply, production, demand forecasting, logistics and sales would have been handled by different teams but Industry 4.0 technologies mean companies can better collaborate transparently and improve end-to-end visibility.
- Production: the ability to create a more seamless and safe production process is one of the obvious benefits of Industry 4.0. Digital enhancements such as machine-vision algorithms and wearable technologies are allowing staff to maintain safe distances as operations restart, while data collection and analysis are being automated to reduce errors and inaccuracies and, in turn, speed up the monitoring and evaluation of workforce performance and quality assurance. Boosting employee safety, operational efficiencies and product quality is the aim of any executive and Industry 4.0 technologies are putting that goal within reach.
- Delivery: once a manufacturer has produced quality goods, it is time to ensure swift and efficient delivery and automation continues to enhance the process. Shuttle systems, automated retrieval systems, smart shelves and drones are just some of the Industry 4.0 technologies improving inventory inspection, while digital and analytics solutions are making it easier to track the delivery of goods.
Industry 4.0 challenges and risks
We have spoken a lot about the benefits of adopting Industry 4.0 technologies but any revolution can present challenges and risks for businesses. The good news is that such hurdles can be overcome with awareness and planning.
- Lack of skills: one of the biggest issues highlighted by companies pursuing digital transformation is a lack of access to skilled personnel. This is especially so when it comes to user interface, data science, software development and machine-level controls, with many adopters expressing challenges associated with finding, training and reskilling staff. The fear of the unknown can also see many existing team members reluctant to use new digital tools and applications. For these reasons, companies may benefit from conducting a training needs analysis to identify how to empower their teams.
- Data and IT security: while digital innovation has undoubtedly improved business efficiencies, it has also opened organizations up to the threat of security breaches and data leaks. When most people hear the term ‘IT security’, they think of cyberattacks but other threats that can lead to operational disruptions include network misconfigurations, software failures and erroneous commands. The move to an Industry 4.0 setting also requires IT infrastructure to be capable of handling the extra connectivity required for one’s digital transformation.
- Cultural change: a vital aspect of any successful revolution is the willingness of people to embrace the cause and it is no different with Industry 4.0. If employees are resistant or even hesitant to adapt to change, digital transformation can stall before it even gets started. Prepare staff for such change and seek their buy-in to give your project every chance of success. Likewise, seek advocates from a senior or executive level to ensure there are leaders helping drive the cultural change needed for success.
- Investment: digital revolution requires significant long-term capital investment but organizations should not be scared off by that thought. Rather than commit to a large initial influx of cash, companies can think big but start small with a simple – and achievable – solution that sets the base for further innovation. Identify a smart solution that can deliver an instant win and build the confidence an organization needs to implement further Industry 4.0 technologies.
Tips for industry 4.0 implementation
If we could offer just one piece of advice for adopting Industry 4.0 technologies, it would be to start small and keep things simple. That said, there are several other tips worth adhering to when undertaking a digital transformation.
Assess your readiness
Digital transformation is the way forward for any business but do not make the mistake of rushing to the start line. Take the time to assess your readiness for adopting Industry 4.0 technologies and how they will impact your operations by using digital readiness tools that provide insights about what areas of a business to initially focus on.
Develop a digital roadmap
Digital transformation requires the dedicated focus of any major strategic plan. For that reason, organizations should invest the time and resources needed to map out their digital plans and truly understand how they will impact various areas across a business. Target technology, processes, skills and training, along with setting clear expectations for working hand-in-hand with suppliers, customers and partners.
Be practical
Industry 4.0 technologies are good in theory but preparing for the practicalities of digital transformation is where the real success will come from. Recruit the people you need to deliver change or identify how to develop them from within the business. Enhance digital infrastructure, source investment capital and secure the resources needed to deliver the results you are after.
Think long-term
While it’s important for many organizations to start small and simple, they should never take their eyes off long-term opportunities for digital innovation. There is no such thing as an overnight revolution and that is why it is crucial to remember that true transformation takes time. Short-term wins are great but long-term thinking is where true revolution will be found.
Invest wisely
Do not make the mistake of investing in technology for the sake of simply doing so. Industry 4.0 tools are the way of the future but not all of them will deliver the same returns for all companies. To realize the best impact for your business, clearly identify your transformation goals, research the best technologies to achieve them and always remain focused on aligning actions with your specific strategy.
What does the future hold?
The term ‘Industry 4.0’ had its genesis in Germany in 2011. First coined as a high-tech government initiative, it was shared for the first time with the wider world in the same year at the Hannover Fair and quickly caught the imagination of leaders in academia and government. Little more than a decade later and Industry 4.0 is now the talk of the industry as business leaders rush to ensure their organizations do not miss out on the obvious benefits of the revolution.
While it will be many years until the true long-term impacts are known, there is no denying the signs are promising that Industry 4.0 will deliver similar boosts to previous industrial revolutions. One only need look at the fact that U.S. productivity in the second and third quarters of 2020 rose a collective 15.2% - the largest six-month improvement since 1965 – to know incredible gains are being made.
The COVID-19 pandemic is also playing a huge role, with companies stepping up the speed of their digital transformations to adapt to a new workplace landscape. Where once it might have taken years for executives to embrace new technologies, the likes of social distancing and remote work have forced them to not only accept change but embrace it. As one survey found, companies are three times more likely to conduct at least 80% of their customer interactions digitally than they were before the crisis.
While some revolutions should justifiably be feared, Industry 4.0 is not one of them. The fourth industrial revolution is a chance for organizations to improve business procedures, streamline operations and foster an environment for happier staff and customers. Now is the right time for leaders, managers and business owners to discuss the adoption of Industry 4.0 technologies with their teams and independent experts and implement the perfect solutions for their situations.
Just as Industry 4.0 has entered the business lexicon, ‘The Great Resignation’ is a concept that is attracting attention from executives and scholars alike. Discover the lessons organizations can take from the phenomenon to reimagine how their offices operate, reassess their values and culture and increase their candidate and employee ‘likeability’.